No Blog Eletrônica de Potência você encontrará informações sobre teses,artigos,seminarios,congressos,tecnologias,cursos,sobre eletrônica potência. “TEMOS O DESTINO QUE MERECEMOS. O NOSSO DESTINO ESTA DE ACORDO COM OS NOSSOS MERITOS” ALBERT EINSTEIN. Imagination is more important than knowledge, for knowledge is limited while imagination embraces the entire world. EL FUTURO SE CONSTRUYE HOY,EL SUCESSO NO ES FRUTO DE LA CASUALIDAD,SE HUMILDE ,APRENDE SIEMPRE CADA DIA.
AUTOR DO BLOG ENG.ARMANDO CAVERO MIRANDA SÃO PAULO BRASIL
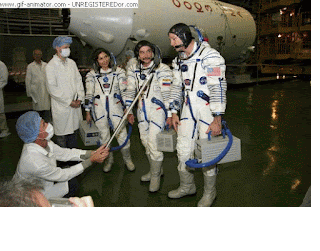
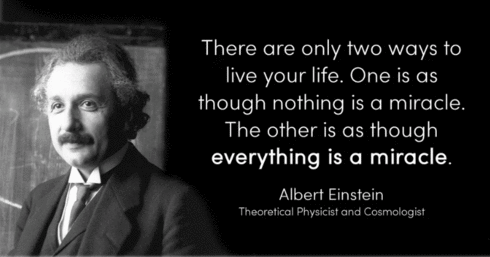.gif)
“SE SEUS PROJETOS FOREM PARA UM ANO,SEMEIE O GRÂO.SE FOREM PARA DEZ ANOS,PLANTE UMA ÁRVORE.SE FOREM PARA CEM ANOS,EDUQUE O POVO.”
“Sixty years ago I knew everything; now I know nothing; education is a progressive discovery of our own ignorance. Will Durant”

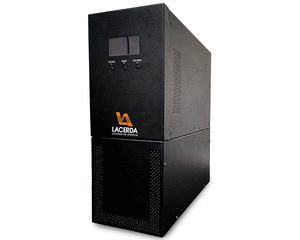
https://picasion.com/
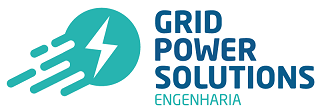
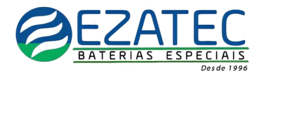
segunda-feira, 16 de dezembro de 2013
Power Factor Correction of Single-phase Boost Converter for Low-cost Type UPS Configuration Jong-Chan Park․Jin-Geun Shon
Power Factor Correction of Single-phase Boost Converter for Low-cost Type UPS Configuration 박 종 찬*․손 진 근† (Jong-Chan Park․Jin-Geun Shon) The Transactions of the Korean Institute of Electrical Engineers Vol. 62P, No. 3, pp. 145~150, 2013
Abstract -A novel AC to DC PWM converters with unity input power factor are proposed to overcome the above shortcoming. The main function of these converters is to shape the input line current to force it exactly in phase with the input AC voltage. Therefore, the input power factor can be improved to near unity and the input current harmonics can be eliminated. In this paper, half-bridge converter with two active switches and two diodes are utilized for low-cost type UPS configuration. By having only two semiconductors in the current path at any time, losses can be reduced over the conventional boost topology. Also, this converter provides controllable dc-link voltage, high power factor, and low cost type converter by simple power circuits. Simulation results show that the proposed half-bridge converter/inverter control technique can be applied to single-phase low-cost type UPS systems successfully.
LINK
http://www.koreascience.or.kr/article/ArticleFullRecord.jsp?cn=DHJGHA_2013_v62n3_145
https://www.mediafire.com/?fqu14xattw5nwkp
LLC Resonant Converter design for Uninterruptible Power Supply Battery Discharger
DOWNLOAD
http://www.koreascience.or.kr/article/ArticleFullRecord.jsp?cn=JRJJC3_2013_v18n3_240
https://www.mediafire.com/?143thdj9xfgg61s
A Controller Design for a Stability Improvement of an On-Board Battery Charger Hae-Gwang Jeong* and Kyo-Beum Lee†
A Controller Design for a Stability Improvement of an On-Board
Battery Charger
Hae-Gwang Jeong* and Kyo-Beum Lee†
Corresponding Author: Department of Electrical and Computer
Engineering, Ajou University, Suwon, Korea. (kyl@ajou.ac.kr)
* Dept. of Electrical and Computer Engineering, Ajou University,
Suwon, Korea. (lite88@ajou.ac.kr)
Received: May 27, 2013; Accepted: June 7, 2013
Abstract – This paper proposes the controller design for a stability improvement of an on-board
battery charger. The system is comprised of a power factor correction (PFC) circuit and phase shift
full-bridge DC-DC converter. The PFC circuit performs the control of the DC-link voltage and the
input power factor. The DC-DC converter regulates the voltage and the current in the battery using the
DC-link voltage. This paper proposes the design method of PI controller for the PFC circuit using a
small signal model. The analysis and design of a type-three controller for the DC-DC converter is also
presented. A simulation and experiment has been performed on the on-board battery charger and their
results are presented to verify the validity of the proposed system.
DOWNLOAD
http://www.koreascience.or.kr/article/ArticleFullRecord.jsp?cn=E1EEFQ_2013_v8n4_951
https://www.mediafire.com/?b466cwi2g7t404z
Battery Charger
Hae-Gwang Jeong* and Kyo-Beum Lee†
Corresponding Author: Department of Electrical and Computer
Engineering, Ajou University, Suwon, Korea. (kyl@ajou.ac.kr)
* Dept. of Electrical and Computer Engineering, Ajou University,
Suwon, Korea. (lite88@ajou.ac.kr)
Received: May 27, 2013; Accepted: June 7, 2013
Abstract – This paper proposes the controller design for a stability improvement of an on-board
battery charger. The system is comprised of a power factor correction (PFC) circuit and phase shift
full-bridge DC-DC converter. The PFC circuit performs the control of the DC-link voltage and the
input power factor. The DC-DC converter regulates the voltage and the current in the battery using the
DC-link voltage. This paper proposes the design method of PI controller for the PFC circuit using a
small signal model. The analysis and design of a type-three controller for the DC-DC converter is also
presented. A simulation and experiment has been performed on the on-board battery charger and their
results are presented to verify the validity of the proposed system.
DOWNLOAD
http://www.koreascience.or.kr/article/ArticleFullRecord.jsp?cn=E1EEFQ_2013_v8n4_951
https://www.mediafire.com/?b466cwi2g7t404z
A Three-Phase High Frequency Semi-Controlled Battery Charging Power Converter for Plug-In Hybrid Electric Vehicles
A Three-Phase High Frequency Semi-Controlled
Battery Charging Power Converter for Plug-In
Hybrid Electric Vehicles
Mahmoud M. Amin and Osama A. Mohammed†
† Dept. of Electrical and Computer Eng., Florida International University, Florida, United States
Abstract
This paper presents a novel analysis, design, and implementation of a battery charging three-phase high frequency semicontrolled
power converter feasible for plug-in hybrid electric vehicles. The main advantages of the proposed topology include
high efficiency; due to lower power losses and reduced number of switching elements, high output power density realization, and
reduced passive component ratings proportionally to the frequency. Additional advantages also include grid economic utilization
by insuring unity power factor operation under different possible conditions and robustness since short-circuit through a leg is not
possible. A high but acceptable total harmonic distortion of the generator currents is introduced in the proposed topology which
can be viewed as a minor disadvantage when compared to traditional boost rectifiers. A hysteresis control algorithm is proposed
to achieve lower current harmonic distortion for the rectifier operation. The rectifier topology concept, the principle of operation,
and control scheme are presented. Additionally, a dc-dc converter is also employed in the rectifier-battery connection. Test results
on 50-kHz power converter system are presented and discussed to confirm the effectiveness of the proposed topology for PHEV
applications.
LINK DOWNLOAD
http://www.koreascience.or.kr/article/ArticleFullRecord.jsp?cn=E1PWAX_2011_v11n4_490
Battery Charging Power Converter for Plug-In
Hybrid Electric Vehicles
Mahmoud M. Amin and Osama A. Mohammed†
† Dept. of Electrical and Computer Eng., Florida International University, Florida, United States
Abstract
This paper presents a novel analysis, design, and implementation of a battery charging three-phase high frequency semicontrolled
power converter feasible for plug-in hybrid electric vehicles. The main advantages of the proposed topology include
high efficiency; due to lower power losses and reduced number of switching elements, high output power density realization, and
reduced passive component ratings proportionally to the frequency. Additional advantages also include grid economic utilization
by insuring unity power factor operation under different possible conditions and robustness since short-circuit through a leg is not
possible. A high but acceptable total harmonic distortion of the generator currents is introduced in the proposed topology which
can be viewed as a minor disadvantage when compared to traditional boost rectifiers. A hysteresis control algorithm is proposed
to achieve lower current harmonic distortion for the rectifier operation. The rectifier topology concept, the principle of operation,
and control scheme are presented. Additionally, a dc-dc converter is also employed in the rectifier-battery connection. Test results
on 50-kHz power converter system are presented and discussed to confirm the effectiveness of the proposed topology for PHEV
applications.
LINK DOWNLOAD
http://www.koreascience.or.kr/article/ArticleFullRecord.jsp?cn=E1PWAX_2011_v11n4_490
A Study on the Hot Spot Temperature in 154kV Power Transformers Dong-Jin Kweon†, Kyo-Sun Koo*, Jung-Wook Woo* and Joo-Sik Kwak*
A Study on the Hot Spot Temperature in 154kV Power Transformers
Dong-Jin Kweon†, Kyo-Sun Koo*, Jung-Wook Woo* and Joo-Sik Kwak*
Abstract – The life of a power transformer is dependent on the life of the cellulose paper, which
influenced by the hot spot temperature. Thus, the determination of the cellulose paper’s life requires
identifying the hot spot temperature of the transformer. Currently, however, the power transformer
uses a heat run test is used in the factory test to measure top liquid temperature rise and average
winding temperature rise, which is specified in its specification. The hot spot temperature is calculated
by the winding resistance detected during the heat run test. This paper measures the hot spot
temperature in the single-phase, 154kV, 15/20MVA power transformer by the optical fiber sensors and
compares the value with the hot spot temperature calculated by the conventional heat run test in the
factory test. To measure the hot spot temperature, ten optical fiber sensors were installed on both the
high and low voltage winding; and the temperature distribution during the heat run test, three
thermocouples were installed. The hot spot temperature shown in the heat run test was 92.6℃ on the
low voltage winding. However, the hot spot temperature as measured by the optical fiber sensor
appeared between turn 2 and turn 3 on the upper side of the low voltage winding, recording 105.9℃.
The hot spot temperature of the low voltage winding as measured by the optical fiber sensor was 13.3℃
higher than the hot spot temperature calculated by the heat run test. Therefore, the hot spot factor (H)
in IEC 60076-2 appeared to be 2.0.
LINKS DOWNLOAD
http://www.koreascience.or.kr/article/ArticleFullRecord.jsp?cn=E1EEFQ_2012_v7n3_312
https://www.mediafire.com/?skoajdlchdtoj0c
Dong-Jin Kweon†, Kyo-Sun Koo*, Jung-Wook Woo* and Joo-Sik Kwak*
Abstract – The life of a power transformer is dependent on the life of the cellulose paper, which
influenced by the hot spot temperature. Thus, the determination of the cellulose paper’s life requires
identifying the hot spot temperature of the transformer. Currently, however, the power transformer
uses a heat run test is used in the factory test to measure top liquid temperature rise and average
winding temperature rise, which is specified in its specification. The hot spot temperature is calculated
by the winding resistance detected during the heat run test. This paper measures the hot spot
temperature in the single-phase, 154kV, 15/20MVA power transformer by the optical fiber sensors and
compares the value with the hot spot temperature calculated by the conventional heat run test in the
factory test. To measure the hot spot temperature, ten optical fiber sensors were installed on both the
high and low voltage winding; and the temperature distribution during the heat run test, three
thermocouples were installed. The hot spot temperature shown in the heat run test was 92.6℃ on the
low voltage winding. However, the hot spot temperature as measured by the optical fiber sensor
appeared between turn 2 and turn 3 on the upper side of the low voltage winding, recording 105.9℃.
The hot spot temperature of the low voltage winding as measured by the optical fiber sensor was 13.3℃
higher than the hot spot temperature calculated by the heat run test. Therefore, the hot spot factor (H)
in IEC 60076-2 appeared to be 2.0.
LINKS DOWNLOAD
http://www.koreascience.or.kr/article/ArticleFullRecord.jsp?cn=E1EEFQ_2012_v7n3_312
https://www.mediafire.com/?skoajdlchdtoj0c
Assinar:
Postagens (Atom)