No Blog Eletrônica de Potência você encontrará informações sobre teses,artigos,seminarios,congressos,tecnologias,cursos,sobre eletrônica potência. “TEMOS O DESTINO QUE MERECEMOS. O NOSSO DESTINO ESTA DE ACORDO COM OS NOSSOS MERITOS” ALBERT EINSTEIN. Imagination is more important than knowledge, for knowledge is limited while imagination embraces the entire world. EL FUTURO SE CONSTRUYE HOY,EL SUCESSO NO ES FRUTO DE LA CASUALIDAD,SE HUMILDE ,APRENDE SIEMPRE CADA DIA.
AUTOR DO BLOG ENG.ARMANDO CAVERO MIRANDA SÃO PAULO BRASIL
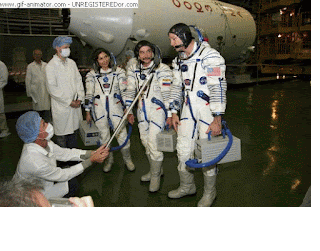
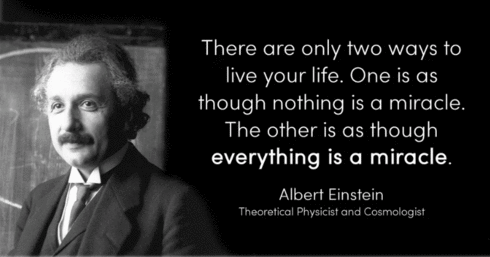.gif)
“SE SEUS PROJETOS FOREM PARA UM ANO,SEMEIE O GRÂO.SE FOREM PARA DEZ ANOS,PLANTE UMA ÁRVORE.SE FOREM PARA CEM ANOS,EDUQUE O POVO.”
“Sixty years ago I knew everything; now I know nothing; education is a progressive discovery of our own ignorance. Will Durant”

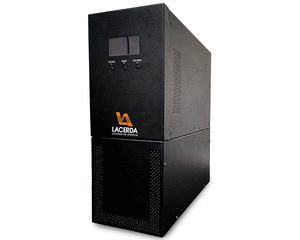
https://picasion.com/
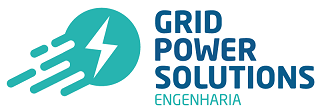
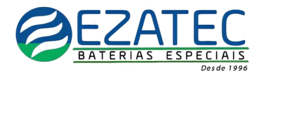
quarta-feira, 28 de março de 2018
A Study on the Wireless Parallel Operation of a Three-phase Modular UPS Inverter Seon – Tae Kim Department of Electrical Communication System Engineering Graduate School of Soonchunhyang University Asan, Korea
A Study on the Wireless Parallel Operation of a Three-phase Modular UPS Inverter Seon – Tae Kim Department of Electrical Communication System Engineering Graduate School of Soonchunhyang University Asan, Korea (Supervised by Professor Jun–Keun Ji)
This paper proposes a wireless parallel operation method of three-phase modular UPS inverter using resistive droop control. Control schemes for the parallel operation of UPS inverters can be classified into two types depending on the presence or absence of the communication line. In this paper, the wireless droop control method is used to overcome the disadvantages of the parallel operation method using communication line. Line impedance of low voltage grid such as parallel UPS inverter system is predominantly resistive. Hence, this paper uses resistive droop control method. And it uses the method holding the system frequency on 60 by applying Q-f(reactive power-phase angle) droop control that takes phase angle instead of frequency of output voltage. Furthermore, it applies a virtual resistor to droop control so that the output impedance of UPS inverter gets closer to resistive. It makes resistive droop control effective. This paper considers modular UPS using three-phase four-wire three-level NPC inverter. Because of symmetry of the circuit configuration, it can be modeled as a separate single-phase three-level inverter. From this, PR voltage controller with excellent control characteristics in single-phase inverter and PI current controller is used. The simulation using PSIM was performed in order to verify the validity of proposed algorithm. After consisting two-parallel system with three-phase modular UPS inverter, the experiment according to resistive load was conducted. It demonstrated the performance of current sharing and power sharing.
sábado, 10 de março de 2018
A Study on the Wireless Parallel Operation of a Single-phase UPS Inverter using Single-loop Robust Voltage Controller Dae-kwan Ku Department of Electrical Communication System Engineering Graduate School of Soonchunhyang University South Korea
A Study on the Wireless Parallel Operation of a Single-phase UPS Inverter using Single-loop Robust Voltage Controller Dae-kwan Ku Department of Electrical Communication System Engineering
Graduate School of Soonchunhyang University Asan, South Korea
(Supervised by Professor Jun - Keun Ji, Guee - Soo Cha)
ABSTRACT
This paper proposes a wireless parallel operation method of single-phase UPS inverter using single-loop robust voltage controller and resistive droop control. Conventional parallel operation methods of UPS inverter using communication line are that such as centralized control, master-slave(MS), average current sharing(ACS), and circular chain control(3C). Although these methods achieve both good THD of output voltage and equal current sharing, but they need communication line. Therefore could reduce the system reliabilty and expandability. The wireless parallel operation such as droop control is suitable method to overcome for demerits of parallel operation methods using communication line. The droop control method don't need communication line because it uses only local power measurements. Thus droop control method is proper method for parallel operation of modular UPS. Conventional P-ω, Q-E inductive droop control method is derived from the assumption that UPS inverter output impedance is pure inductive. Therefore it's not proper method for low voltage grid such as parallel UPS inverter system. Hence, this paper uses P-E, Q-ω resistive droop control method. This method is derived from the assumption that UPS inverter output impedance is pure resistive. In addition, a single-loop robust voltage controller is used for the UPS inverter. The single-loop voltage controller can reduce material cost owing to the decrease of current sensor in the UPS system. Then simulations and experiments for the two-parallel system of single-phase UPS inverters with resistive and nonlinear loads demonstrate the feasibility of proposed parallel operation method providing improved performance - good output voltage control and equal power sharing. Key words : UPS inverter, parallel operation, robust voltage control, droop control.
A Study on the Heat Flow Inside UPS according to the Outside Temperature Dong – Min Kim Department of Mechanical Engineering, The Graduate School Konyang University
A Study on the Heat Flow Inside UPS according to the Outside Temperature Dong – Min Kim
Department of Mechanical Engineering, The Graduate School Konyang University
Nonsan Chungnam Korea
(Supervised by Professor Young-Sik Yoon)
ABSTRACT
UPS is an electrical apparatus that provides emergency power to a load when the input power source, typically mains power, fails. When installing UPS in outdoors (a road near or mountain, etc..), it is also possible many problems according to the outdoor environment. And it is possible generate condensation by a temperature difference The purpose of this study was to predict the inner temperature of UPS and to prevent dew condensation in UPS by simulating the heat flow using ANSYS. So in this study, The inner heat flow simulations for UPS were conducted by the Computation Fluid Dynamics Analysis, ANSYS, during the active state of UPS. Compared with Air temperature, Relative humidity, Inner temperature of UPS to be found that condensation is occurring. It’s can be improved by ventilation or insulation effectively inside UPS according to this simulation result.
LINK
http://www.mediafire.com/file/qoeywubv5dful8a/A_Study_on_the_Heat_Flow_Inside_UPS_according_to_the_Outside_Temperature.pdf
quarta-feira, 28 de fevereiro de 2018
The design of a Inverter and DSP controller for the driving of BLDC motor used in Small Electrical Vehicle -Kim, Jae Woo Dept. of Electronic Engineering Graduate School of Changwon National University
The design of a Inverter and DSP controller for the driving of BLDC motor used in Small Electrical Vehicle
Kim, Jae Woo
Dept. of Electronic Engineering Graduate School of Changwon National University
ABSTRACT
This paper mainly handles about the designing of the inverter and the controller to drive the BLDC motor for the small electric vehicle. The speed control part of driving system is designed to select the usage of 32 bits DSP(TMS320F2808) specialized for a servo motor control and 16 bits Microchip’s micro-processer(dsPIC30F2010) optionally. The inverter driving part is designed with the MOSFET(IRFB3077) which is capable of high speed switching and better for low voltage batteries switching. Instead of using complicated PWM(Pulse width Modulation) method, we used simple 3 phase, 2 excitation PWM method having 6 step excitation sequence and voltage controlled PWM method to reduce the load of a software. The digital control algorithm for the speed control is simplified to control the speed by controlling voltage right away not performing current control. Through the result obtained from the driving of the BLDC motor by using the suggested hardware controller and algorithm for speed and PWM, we proved the usefulness of the hardware controller and control algorithm. KEYWORDS BLDC motor, electric vehicle, inverter, micro-processer, MOSFET, PWM, control algorithm.
terça-feira, 20 de fevereiro de 2018
Design and Testing of Voltage Source Inverter and Motor Control System for Electric Vehicle Lars Helge Opsahl Norwegian University of Science and Technology Department of Electric Power Engineering
Design and Testing of Voltage Source Inverter and Motor Control System for Electric Vehicle
Lars Helge Opsahl
Norwegian University of Science and Technology
Department of Electric Power Engineering
Abstract
With fast rotating permanent-magnet motors and compact battery storage units, the high performance motorsport community has, in recent years, started to utilize the quick response and high torque of electrical drivetrain solutions. By recovering energy, braking into a corner, for then to utilize the same energy, boosting out again, the electrical machine gives increased performance even for the fastest racing cars. The purpose of the work presented in this Master’s thesis is to develop and produce the power electronics and motor control system needed to control such an electric machine, where the final product is used to drive a fully electric prototype racing car. The thesis presents the conceptual work, design choices, prototyping, testing and development of a 2-level voltage source inverter and motor control system. The voltage source is a battery accumulator energy storage unit, while the machine is a three-phase permanent-magnet motor. The voltage source inverter is based on insulated-gate bipolar transistors (IGBTs), controlled by a motor control system called field oriented control. On command from the driver’s throttle, the motor control system generates the required stator currents, giving the wanted output torque, supplied from the voltage source of the battery accumulator. The inverter is the connecting interface between the power source, and the rotating machinery. With the amount of energy and power needed to drive a racing car, safe and reliable operation is important. To ensure the safety of the driver and operating personnel, the system and its safety features have been through extensive testing in a laboratory setup and on the race tracks. In the system development process, simulation and modelling tools have been applied to investigate different solutions and technologies. These tools have also been used to design the electric circuits, program code and mechanical design needed for the system. The final product is installed in a racing car and shows great performance.
LINK
https://brage.bibsys.no/xmlui/bitstream/handle/11250/2368215/13287_FULLTEXT.pdf?
Assinar:
Postagens (Atom)